Brown Betty
The refreshing detail of a perfectly comfortable pour
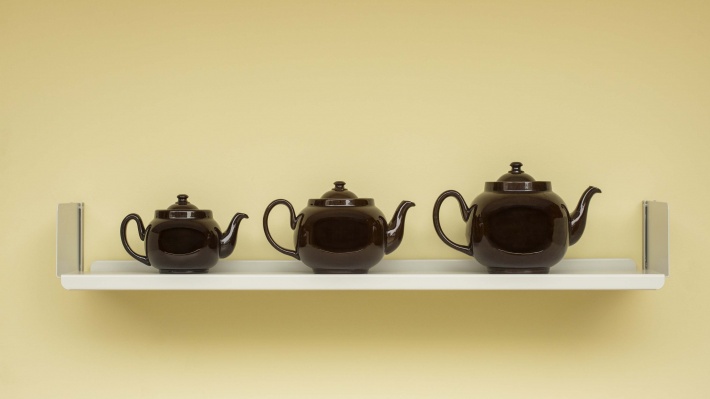
Words: Vitsœ
Photography: Bjarte Bjørkum, Angela Moore, Vitsœ
“The chances are, if I asked you to draw a teapot from memory, you’d think of a shape not too dissimilar from the Brown Betty. That’s because it’s one of the most manufactured teapots in British history.” So says ceramicist Ian McIntyre who, as part of his Collaborative Doctoral Award with Manchester School of Art, York Art Gallery and the British Ceramics Biennial, set about examining the origins of this noble pot.
Brown Betty is a product of evolution, with form and function refined over decades, rather than the authorship of any single designer. It emerged as a cheap, utilitarian pot for the working classes, absorbed into the fabric of everyday life. This evolution resulted in a teapot modest in appearance yet perfect for the task in hand: brewing and pouring tea. By quietly performing its job so well it has endeared itself to generations. Despite its popularity however, surprisingly little is known about the teapot’s original makers.
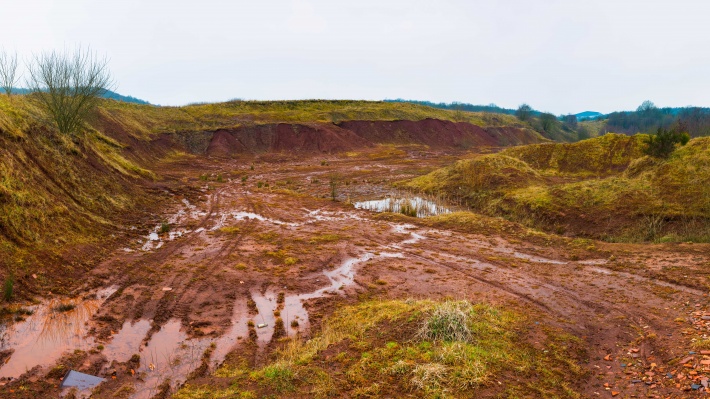
The very character of the pot comes from the quality of the clay, which has been mined in Staffordshire for red-ware teapots for over 300 years. “I think it’s safe to say that a Brown Betty that isn’t made of Staffordshire red clay, isn’t an original Brown Betty at all” states Ian. This clay – Etruria Marl – was first refined around 1695 by two Dutch brothers, John Philip Elers and David Elers, in Bradwell Woods, North Staffordshire. Prior to this the potteries which existed were small family-run outfits, producing crude wares like butter pots for farmers to transport their produce to market.
The brothers used this clay to make teapots to emulate and compete with the expensive red stoneware Yixing teapots, which were being imported from China by the East India Company. It is widely agreed that the refinement of this clay, which could reliably withstand the temperature of boiling water without cracking, gave rise to new technological experiment in Staffordshire, and became a key catalyst for the industrialisation of the six towns that make up Stoke-on-Trent.
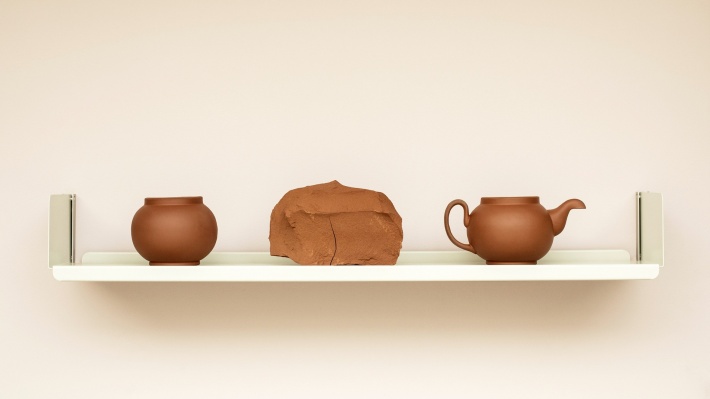
The Brown Betty is a purely rational design, stripped of anything superfluous to its function and production methods” explains Ian, who over the course of his studies sourced multiple Brown Bettys of various shapes, dates and manufacturer to evaluate the principles behind the design transformation. He discovered that over the years the Brown Betty form migrated into a globe, which was seen as the best shape to infuse the loose-leaf tea when water was added. The shape and the wall-thickness combine to keep the tea warm.
The most innovative maker of Brown Betty was Alcock, Lindley and Bloore, who operated through the 20th century. The body of an Alcock, Lindley and Bloore teapot was made in three parts. The globe was pressed before the handle and spout were applied. This enabled a potter to crudely punch a grid of holes into the globe before attaching the spout. The grid held the tea leaves in the globe when pouring. These are details which the Brown Betty sadly lost over the years, as they were cast in one-piece moulds to reduce manufacturing costs. Ian, however, saw these details as fundamental to the authenticity of Brown Betty and set about making pots of his own to further understand the delicacy of the design detail.
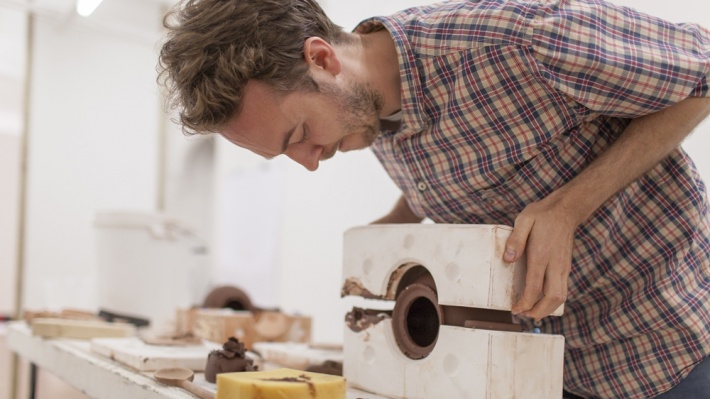
He discovered that the handle presented a functional and ergonomic shape, with the generous loop positioning the gripping hand for easy leverage of the pot. This also minimised the strain on the wrist – when pouring and the return at the top of the loop prevented knuckles burning on the globe. At first sight the spout of the historic pots he analysed appeared poorly finished, but they had been rough-cut deliberately by a craftsman. The sharp edges at the opening – and just underneath the lip – cut the flow of water, preventing tea from dribbling back down the outside of the pot. To be certain that tea would not dribble a patented non-drip spout had been introduced as an optional feature. Functioning like a tap the spout ensured a straight pour and almost magically eliminated drips.
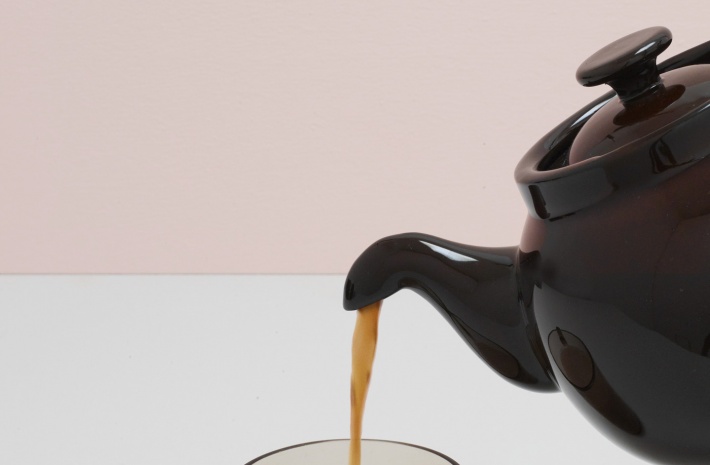
A classic Brown Betty would have been glazed in either the rich brown Rockingham glaze, or a transparent glaze that reveals the natural colour of the clay. Both have the advantage of masking any tea stains on the teapot. If the glaze were chipped, the red colour of the clay would be revealed – favourable to a contrasting clay – allowing a characteristic patina to lengthen the life of the pot. To prevent the lid falling out of the pot while pouring, an ingenious solution was reached: the lid in the tilted pot slid forward into a groove in its collar, locking it in position. When the pot was restored to horizontal, the lid released. A more discreet feature of this patented design enabled pots to be stacked for storage by placing the lid upside down in the pot. To support this feature, the spout and the handle stay below the collar of the pot, which also means the pot could drain upside-down after washing.
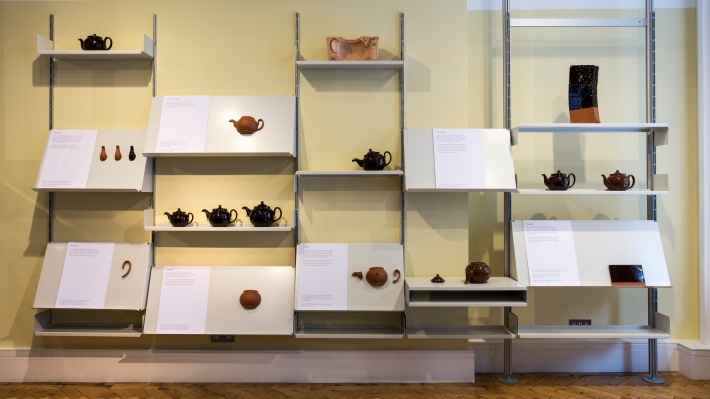
In 2016 Ian’s research into the history of Brown Betty and his practical investigations were presented in an exhibited at Vitsœ’s London shop. He showed moulds made from an original Alcock, Lindley and Bloore teapot and pots cast using Staffordshire red clay. The culmination of this understanding of the form and function of Brown Betty lead to the development of his first prototype Brown Betty.
Following this exhibition, Ian teamed up with Cauldon Ceramics of Staffordshire, a small craft manufacturer of traditional redware and the oldest remaining maker of the Brown Betty teapot in the UK. Together they set about remanufacturing this lustrous beauty. Taking great care to respect the traditions and the years of refinement that have gone before, including the patented locking lid and non-drip spout. Using the authentic clay, the collaboration implemented new production processes and design details to reinstate an authentic representation of a classic Brown Betty.
Ian’s attention to detail has ensured that the traditions of the pot have been maintained. This latest Brown Betty edition is intended to promote the legacy and value of this everyday object that has transcended fashion but is a beautiful and reliable utility object. Or, as Ian says:
“On a personal note I feel that the Brown Betty is a counterpoint to the seemingly unending barrage of new products being launched and discontinued daily in the design industry. I feel that this story reflects a dedication to a material or a design, and the refinement of a process that has given rise to a classic, not because of nostalgia, but because it’s the best at what it does.”
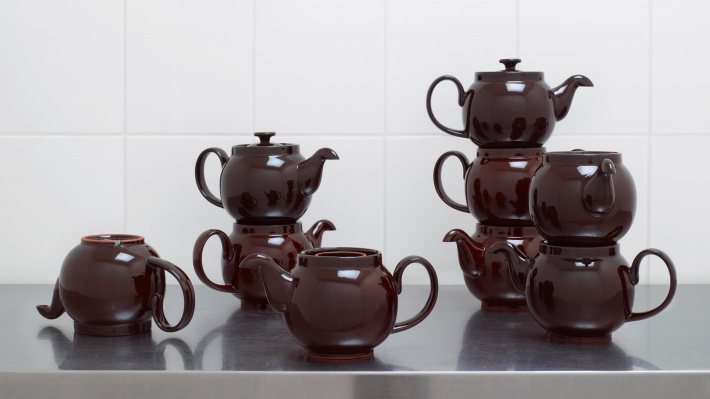
Ian’s latest edition was nominated for the Beazley Design of the Year 2018 at the London Design Museum and is in the permanent collections of London Design Museum, Victoria & Albert Museum, Manchester Art Gallery and York Art Gallery. V&A produced a short film on the Brown Betty, which can be viewed here.
Brown Betty available from Labour and Wait